现代切削刀具材料经历了从碳素工具钢—高速钢,再发展到硬质合金刀——陶瓷刀—PCBN(立方氮化硼)—。
刀具的切削性能越来越好,直接促进了数控加工的极大发展。高速钢刀具热硬性高,有较高的耐磨性、强度和韧性,与硬质合金相比,其最大优点是可加工性好并具有良好的综合力学性能。
由于其良好的性能,目前高速钢仍是世界各国应用最广泛的刀具材料之一。
硬质合金刀具由硬度和熔点很高的碳化物(硬质相)和金属粘接相经粉末冶金方法而制成,其硬度远高于高速钢,在540℃时,硬度仍可达82——87HRA,与高速钢常温时硬度相同。
硬质合金刀具的硬度和韧性随着金属粘接相的含量而变化,一般随着金属相含量的增多,硬度降低而韧性增强。
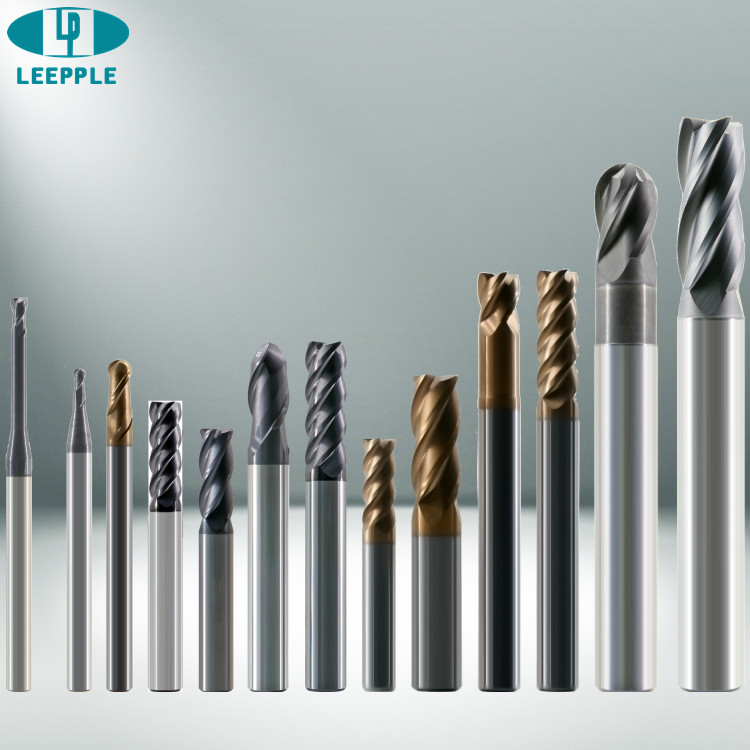
陶瓷刀具研制成功以来,由于其良好的性能,颇受市场欢迎。陶瓷刀具具有硬度高、耐磨性好,摩擦因数低,耐高温、耐热性好等优点,陶瓷刀具已经成为高速切削及难加工材料加工的主要刀具之一。
但是陶瓷刀具抗弯强度低,承受冲击载荷能力较差,当加工面出现凸凹或加工过程振动较大时容易崩刃,不适于在低速和冲击负荷下切削。陶瓷刀具承受热冲击载荷能力较差,切削过程不能使用冷却液,可以实现干式切削。
CBN刀具在硬度和导热率方面仅次于金刚石,具有高的硬度和耐磨性,很高的热稳定性,优良的化学稳定性,较好的热导性,较低的摩擦因数等,基本上具备完美刀具的一切性能,但强度和韧性较差,使用时应避免过大的冲击造成刀具崩刃,因此一般采用负前角高速切削。
CBN刀具昂贵的价格也是制约其普遍使用的重要因素。
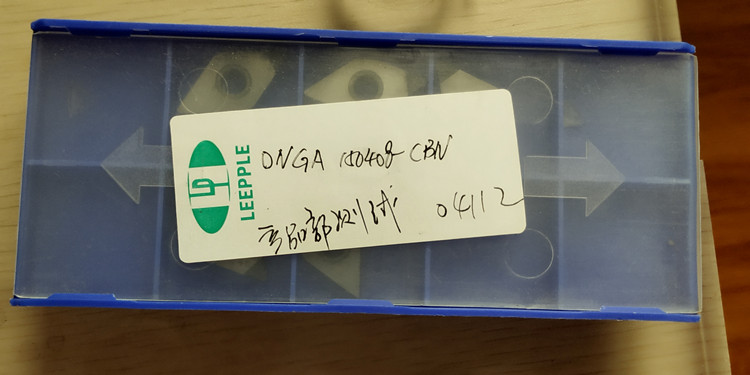
在刀具材料的发展过程中,涂层技术的产生和应用为刀具的强度、硬度和韧性之间的矛盾关系找到了缓解办法,成为切削刀具发展史上的一次革命。刀具涂层技术主要是采用物理或者化学气相沉积的方法,在刀具表面上获得几微米到十几微米厚的硬质膜。
PCD刀具涂层具有高的硬度耐磨性,高的化学稳定性和抗粘结性能,低的摩擦因数等优点。
在PCD刀具基体表面添加涂层,可以很好地解决硬质合金等刀具硬度较软、耐磨性较差、高温时容易氧化等问题。当涂层的性能与基体性能差距较大或与基体材料粘结不牢固时,可以采用多层涂层,逐步改善涂层的韧性、涂层与基体的结合强度、涂层的耐磨性等问题。
涂层技术大大增强刀具硬度、韧性,提高刀具耐磨性和抗氧化性,进而延长刀具使用寿命和改善刀具的切削加工性能。
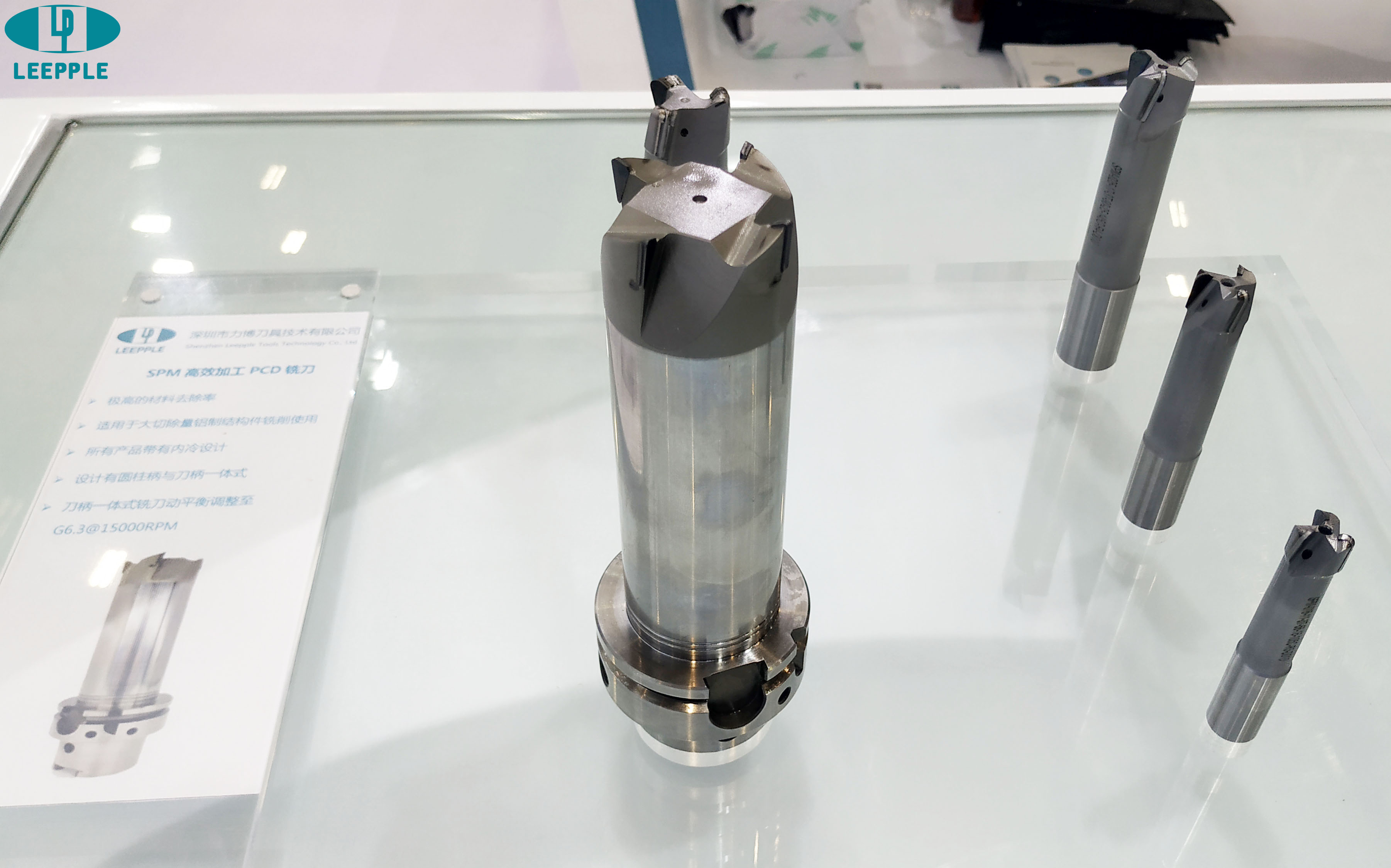